光伏逆變器的工作原理
1、全控型逆變器工作原理:為通常使用的單相輸出的全橋逆變主電路,交流元件采用IGBT管Q11、Q12、Q13、Q14。并由PWM脈寬調(diào)制控制IGBT管的導(dǎo)通或截止。
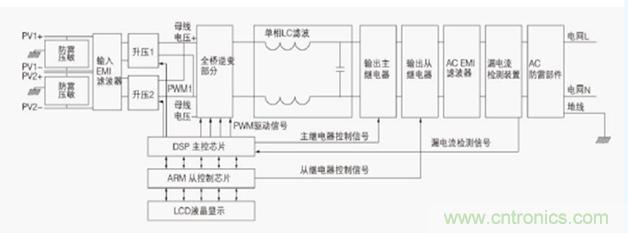
當(dāng)逆變器電路接上直流電源后,先由Q11、Q14導(dǎo)通,Q1、Q13截止,則電流由直流電源正極輸出,經(jīng)Q11、L或感、變壓器初級線圈圖1-2,到Q14回到電源負(fù)極。當(dāng)Q11、Q14截止后,Q12、Q13導(dǎo)通,電流從電源正極經(jīng)Q13、變壓器初級線圈2-1電感到Q12回到電源負(fù)極。此時,在變壓器初級線圈上,已形成正負(fù)交變方波,利用高頻PWM控制,兩對IGBT管交替重復(fù),在變壓器上產(chǎn)生交流電壓。由于LC交流濾波器作用,使輸出端形成正弦波交流電壓。
當(dāng)Q11、Q14關(guān)斷時,為了釋放儲存能量,在IGBT處并聯(lián)二級管D11、D12,使能量返回到直流電源中去。
2、半控型逆變器工作原理:半控型逆變器采用晶閘管元件。Th1、Th2為交替工作的晶閘管,設(shè)Th1先觸發(fā)導(dǎo)通,則電流通過變壓器流經(jīng)Th1,同時由于變壓器的感應(yīng)作用,換向電容器C被充電到大的2倍的電源電壓。按著Th2被觸發(fā)導(dǎo)通,因Th2的陽極加反向偏壓,Th1截止,返回阻斷狀態(tài)。這樣,Th1與Th2換流,然后電容器C又反極性充電。如此交替觸發(fā)晶閘管,電流交替流向變壓器的初級,在變壓器的次級得到交流電。
在電路中,電感L可以限制換向電容C的放電電流,延長放電時間,保證電路關(guān)斷時間大于晶閘管的關(guān)斷時間,而不需容量很大的電容器。D1和D2是2只反饋二極管,可將電感L中的能量釋放,將換向剩余的能量送回電源,完成能量的反饋?zhàn)饔谩?/div>
微逆變器及其核心磁元件
太陽能組件因安裝的位置、烏云狀況、周圍樹葉等陰影的覆蓋等因素的影響,各個組件產(chǎn)生的電力會出現(xiàn)不同程度的離散。如果把它們都串并聯(lián)在一起,就會出現(xiàn)猶如新舊電池組合使用的不良效果。一般電池面積的2~3%被陰影覆蓋時,總的發(fā)電量常常會出現(xiàn)高達(dá)20%的下降,嚴(yán)重影響了整個系統(tǒng)的發(fā)電效能。為此,微逆變器專門對單一的電池組件進(jìn)行獨(dú)立并網(wǎng)發(fā)電,可以最大限度地避免這一問題,此方案一經(jīng)問世便廣受青睞。但一個家庭電力,往往需要十幾個或更多這樣的獨(dú)立逆變單元,因此該逆變器能否實現(xiàn)高效率低成本化就成為影響該系統(tǒng)廣泛應(yīng)用的重要制約因素。
Fig1、2所示微逆變器是比較典型的兩種并網(wǎng)發(fā)電拓?fù)洹ig1中首先采用兩個交錯式臨界工作方式的升壓反激式變壓器,將其占空比按照正弦波半波規(guī)律,通過單級電路的電力的正弦化、隔離升壓和MPPT(MaximumPowerPointTracker)控制濾波,然后再全橋半波工頻換相濾波,高效地實現(xiàn)了低壓直流的直接并網(wǎng)發(fā)電。這是目前最具有潛力的微逆變器工作方式之一。Fig2則是通過全橋隔離升壓、濾波,再進(jìn)行全橋逆變?yōu)V波并網(wǎng)的常規(guī)方式。這種方式的明顯缺點(diǎn)就是需要較多的磁元件,且高頻開關(guān)器件過多,成本和效率方面優(yōu)勢不足,且電路為了簡化,無一例外地采用了硬開關(guān)驅(qū)動,這樣隔離主變壓器的漏感要非常小,一般不得不采用多層電路板扁平變壓器結(jié)構(gòu),使得其寄生電容大,成本高,EMI也比較難處理。
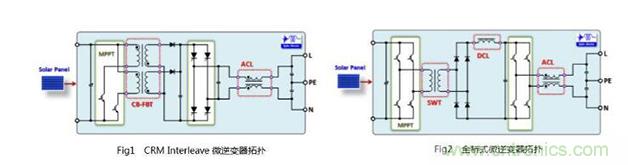
對于主流的CRMInterleave拓?fù)?,核心磁元件有兩種,反激電源變壓器和交流濾波電感ACL。對于反激電源變壓器FBT(FlybackTransformer),由于其工作在臨界模式的數(shù)百kHz的工作頻率,因此此類變壓器的設(shè)計必須遵循如下原則:
1)采用高Bs、高頻低Pcv損耗的鐵氧體磁芯;
2)為了降低變壓器的損耗,需要采用大有效截面、低磁路長度的設(shè)計來控制磁損耗,常用的磁芯有PQ、RM等薄型或是定制化的優(yōu)化形狀的產(chǎn)品;
3)最大限度控制變壓器漏感,采用良好耦合的繞線構(gòu)造;
4)繞線內(nèi)阻盡可能小,同時還必須注意集膚效應(yīng)及氣隙漏磁造成的銅線渦流損耗
對于微逆變器后級濾波的ACL,由于其紋波電流相對較小,一般采用高直流偏置、高頻特性較好的Highflux或性價比更好的NPF環(huán)形鐵硅材料。
住宅型PV逆變器及其核心磁元件
目前廣泛采用的非隔離并網(wǎng)住宅型光伏逆變器,其功率基本上為1.5 KW ~ 6 KW左右。為了實現(xiàn)高的性價比,并最大限度地提高轉(zhuǎn)換效率,業(yè)界甚至采用了SiC半導(dǎo)體、H5拓?fù)洹?電平拓?fù)涞雀鞣N新式技術(shù),但其最基本的拓?fù)洳煌夂鯃D3、4兩種:
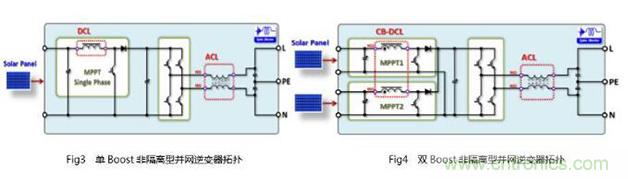
形成這種特點(diǎn)的主要原因,基本上是出于逆變器以及發(fā)電系統(tǒng)的成本和效率考慮:
1)單機(jī)功率比較小(1.5~3 kW)的PV,一般采用單一Boost的MPPT控制;
2)單機(jī)容量超過4 kW的PV,則往往采用雙Boost雙MPPT控制方式;
3)對于一些復(fù)雜系統(tǒng),特別是像日本市場的產(chǎn)品,為適合其國情,往往在PV逆變器的前端會采用多個MPPT的直流升壓,而后端卻只有單Boost進(jìn)行MPPT控制。
住宅型PV中影響整機(jī)效率的被動元件除了EMI濾波器外,上圖中Boost電感和交流濾波電感ACL更因其成本高、效率影響大而成了關(guān)鍵核心磁元件。
另外,薄膜型太陽能電池的大量導(dǎo)入,薄膜型太陽能電池結(jié)構(gòu)存在較大的寄生電容。因此,為了避免因容性漏電而造成的安全問題,這樣的發(fā)電系統(tǒng)還常常采用隔離型的PV逆變。這一方式的一個重要特征是需要采用高頻反激變壓器在Boost電路里實現(xiàn)高頻隔離,或是在Boost之后,再通過LLC諧振或全橋移相零電壓開關(guān)(FB-ZVS)拓?fù)鋪韺崿F(xiàn)高頻的電氣隔離。這樣,高效大功率的反激變壓器、LLC諧振電感和FB-ZVS諧振電感的技術(shù)也成了該類產(chǎn)品重要的核心磁元件。
商用中功率PV逆變器及其核心磁元件
商用中功率PV逆變器輸出功率較大,一般單機(jī)容量在10~50 kW,和住宅型PV類似,工作頻率大多為16~20 kHz。其最明顯的特點(diǎn)是輸出為三相交流,然后再通過3相交流變壓器實現(xiàn)隔離升壓、并網(wǎng)發(fā)電,其典型拓?fù)淙鏔ig5所示。作為濾波用的ACL,則既可以采用3只相同的濾波電感分別濾波,也可以通過3相平衡的耦合電感來提高系統(tǒng)的性價比。
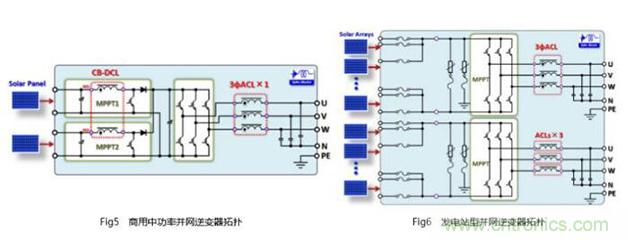
除日本市場以外,作為住宅型非隔離PV逆變器和商用中功率逆變器中的重要核心磁元件的電感,絕大部分采用非晶類磁材。非晶類磁材以其極高的Bs和很好的直流偏置特性,特別適宜于制作大感量的電感。為了進(jìn)一步提供效率,歐洲廠商也研發(fā)了多種的鐵硅類環(huán)形和罐型電感產(chǎn)品。
集中發(fā)電站PV逆變器及其核心磁元件
對于超大面積發(fā)電站式的光伏應(yīng)用,一般均采用比較高的光伏電壓,直接逆變成交流電,通過大功率工頻隔離升壓變壓器實現(xiàn)隔離并網(wǎng)發(fā)電。其代表拓?fù)淙鐖D6所示。
由于該類產(chǎn)品單機(jī)容量大,受到大功率IGBT和高效大功率濾波電感等元件技術(shù)的制約,目前國內(nèi)的產(chǎn)品基本上尚處于2~4 kHz的工作頻率;單機(jī)容量為250~500 kW的功率等級,國際上目前已在9~10 kHz頻率上實現(xiàn)了量產(chǎn)化。
對Boost電感的要求及其解決方案
采用Boost電路的PV逆變器,其功率從1.5 kW~30 kW不等,一般覆蓋了住宅用和商用中功率逆變器的各個等級,該電感的效率的高低,直接決定了逆變器的整機(jī)性能。這樣的電感設(shè)計需要盡可能地減小鐵損和銅損。為了實現(xiàn)這一目標(biāo),簡單的方法就是使用非晶類磁性材料,在保持一定的電感量的情況下盡量降低銅線的內(nèi)阻,其結(jié)果是因用銅量的增加,導(dǎo)致了昂貴的成本。
鑒于Boost升壓電感的工作頻率基于16 kHz~20 kHz的特點(diǎn),電感線圈中的損耗除了直流內(nèi)阻損耗外,交流高頻損耗占有很大的比例。
銅損包含下列四個方面:
1)有效值電流流經(jīng)直流內(nèi)阻的低頻直流損耗;
2)高頻交流分量引起的導(dǎo)線集膚效應(yīng)產(chǎn)生的高頻交流損耗;
3)繞組層間由于高頻電流集膚效應(yīng)作用引起的接近效果高頻損耗;
4)氣隙漏磁經(jīng)過導(dǎo)體形成的渦流損耗
鐵損則主要由磁性材質(zhì)的特性所決定。為了減少鐵損,必須優(yōu)化選取高頻損耗特性好的材料。磁性材料的損耗優(yōu)劣關(guān)系:鐵氧體《非晶《鐵硅鋁《鐵硅《純鐵粉芯。
非晶材料以其極高的抗飽和特性(Bs》1.5T)且高頻損耗優(yōu)于鐵硅鋁的特點(diǎn),本應(yīng)是最好的選擇,但非晶磁致伸縮系數(shù)非常大,常常伴隨較大的噪音;同時,雖然非晶采用厚度為20多μm的帶材加工而成,帶材的渦流損耗非常小,而作為電感磁材料使用時,由于需要開氣隙而不得不切開端面,造成了端面層間的短路。當(dāng)較高的ΔB變化(電感大紋波)出現(xiàn)時,磁芯被切開的端面會出現(xiàn)大的渦流損耗,其實際結(jié)果是磁芯損耗反而遠(yuǎn)遠(yuǎn)高于鐵硅鋁材料的相同ΔB變化下的損耗。由此可見,作為升壓電感的磁性材料,非晶不一定是最好的選擇。
眾所周知,開關(guān)電源高頻化最重要的目的就是通過工作頻率的高頻化,使得電路中的儲能和換能被動元件盡可能地減小,以到達(dá)高效率、低成本、小體積、快響應(yīng)等目的。所以,在保障性能和不增加額外成本的情況下,最大限度地采用盡可能小的電感量,是PV逆變器對Boost電感設(shè)計的基本要求和技術(shù)發(fā)展趨勢。
然而,在不改變頻率的情況下,減小電感量,雖然可以大幅降低成本,但此時的紋波電流也隨之加大,磁性材料內(nèi)部的ΔB的增加,除了明顯增加了非晶的磁芯損耗外,非晶氣隙中的漏磁成分的大幅增加,還直接導(dǎo)致周邊銅繞線的渦流效應(yīng)(感應(yīng)加熱原理)。因此,在使用非晶設(shè)計時,為回避這一問題,不得不靠盡量提高電感量,減小電流紋波來減輕這一負(fù)擔(dān),其結(jié)果,為提高效率不得不增大電感同時壓低內(nèi)阻而使用大量銅材,這是非晶不利于小電感量應(yīng)用的根本原因。
為了應(yīng)對這一問題,一個非常好的方法就是采用鐵氧體+鐵硅鋁等方法(或高性能鐵硅NPF材料),通過混合磁路(Hybrid Magnetics)技術(shù),根據(jù)光伏Boost電流的工作特點(diǎn),揚(yáng)長避短,做到既降低了電感量(小體積、低成本要求),又顯著改善電感的損耗。
面向歐美的光伏逆變器,必須最大限度地改善歐洲效率ηEURO和加州能源效率ηCEC,歐效和CEC綜合效率均為電源的不同負(fù)荷情況下的綜合效率,它們的換算方法如下:
ηEURO=0.03×η5%+0.06×η10%+0.13×η20%+0.1×η30%+0.48×η50%+0.2×η100%ηCEC=0.04×η10%+0.05×η20%+0.12×η30%+0.21×η50%+0.53×η75%+0.05×η100%
從中可知,要顯著提高其綜合效率,就必須最大限度地控制好較輕負(fù)荷時的功率損耗。利用混合磁路中不同磁材的特性,通過對其磁路長度、磁阻及繞線匝數(shù)等影響電感特性的諸要素進(jìn)行優(yōu)化調(diào)節(jié),使之符合圖7所示的L-I直流電感偏置特性,從而可實現(xiàn)歐效改善與低成本設(shè)計的兼顧。
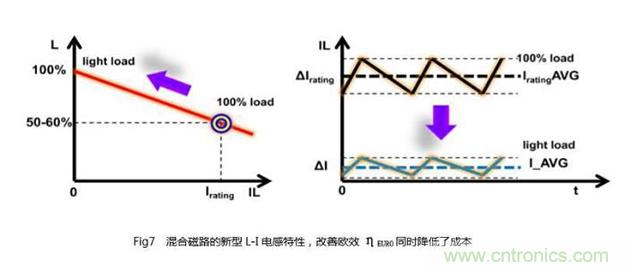
Fig7左圖展示出了Hybrid Magnetics新型電感的L-I特性,其突出特點(diǎn)就是在額定負(fù)載時,通過降低額定電感量,人為加大電路中的電流紋波(利用光伏逆變器輸入端的大容量電容“過剩”的高頻大紋波能力資源),來完成低內(nèi)阻且少用銅的設(shè)計。另外,當(dāng)負(fù)載逐漸減輕時,電感量會隨之大幅提升,使得此時的磁芯內(nèi)部的ΔB明顯下降。這樣,一方面減少了鐵損,另一方面局部的微小氣隙處的漏磁也會大幅減輕,使渦流影響極小。另外,隨著電感量的迅速提升,電感中的高頻電流紋波大幅下降,進(jìn)一步降低了電感電流的有效值和電流的高頻分量,從而使得線圈的直流損耗、集膚效應(yīng)、接近效應(yīng)等明顯改善。實踐證明,這樣的設(shè)計可以使逆變器的整機(jī)效率,從極輕負(fù)載開始就處于高效,直至滿載,個別情況下,較輕負(fù)荷的效率還可能在很寬的一個范圍內(nèi)高于滿載效率。Fig7右圖顯示負(fù)載下降時,電感的紋波電流也明顯下降。
Hybrid Magnetics技術(shù)的一個基本手法,就是在繞組內(nèi)部使用有利于產(chǎn)生電感量和直流偏置特性的高性能鐵硅或鐵硅鋁材料,而在繞組之外,則盡量使用20 kHz頻率下磁芯損耗幾乎可以忽略不計的高性能鐵氧體材料,來盡可能地縮短非繞線部的磁路長度和減小磁阻,同時避免因空氣氣隙處的漏磁而產(chǎn)生的導(dǎo)線的渦流損耗。通過這一手法,可以在比原來非晶型電感量小30~50%的條件下,使得一臺5kW的光伏逆變器整機(jī)效率提高0.5~0.7%以上(即滿功率時減少30W左右的電感發(fā)熱)。
對于功率大的PV逆變器,因其常常采用雙Boost的結(jié)構(gòu),為此若進(jìn)一步引入2合一式的磁集成(Integrated Magnetics)技術(shù),還可以進(jìn)一步提高效率,降低成本。
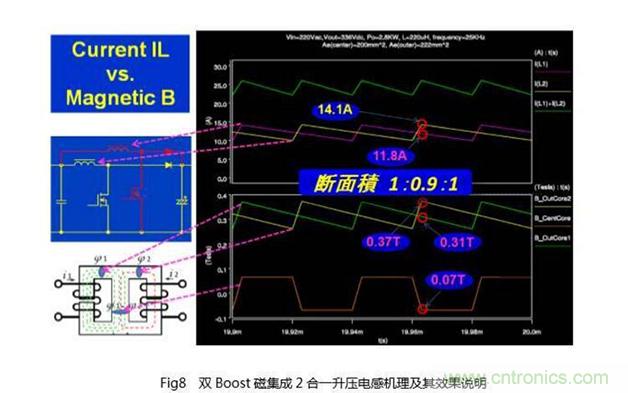
如圖8所示,磁集成電抗器是由兩個獨(dú)立的電感線圈,分別繞制在磁芯的兩個臂上,再通過其中公用的中間磁路形成磁集成的工作原理。兩線圈中流過圖示方向的電流時,兩線圈所產(chǎn)生的磁束,會在中間公共部分磁芯里進(jìn)行磁通量抵消,甚至為零。如果在同一時刻流過線圈的電流值相接近時,磁芯公共部分的磁通可互相抵消,即便磁芯的有效截面積小,因其總磁通量很小,此處的磁場強(qiáng)度B也會很低。由于兩臂的有效截面和中心柱的有效截面積之比被設(shè)計在1:0.9,中心柱磁芯也遠(yuǎn)不會飽和。
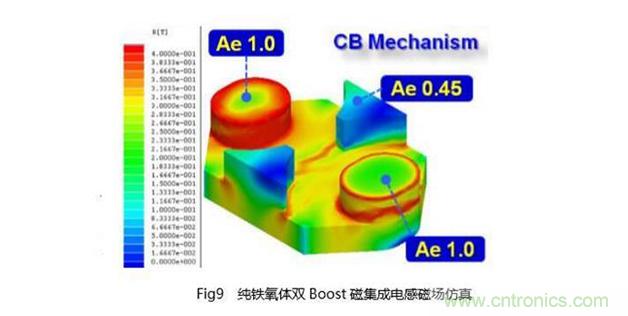
圖9為該電感在上述條件下,讓左邊線圈電流最大,使磁芯接近飽和的仿真結(jié)果。從圖中可以明顯看出,即便兩邊的磁芯接近飽和,中間公共部分磁芯的截面雖小,卻仍遠(yuǎn)離飽和。此時磁芯即便是處于高頻工作狀態(tài),中間磁芯柱上的ΔB非常小,這部分磁芯的損耗自然也很低。
對交流濾波電感的要求及其解決方案
光伏逆變器的濾波電感的根本作用在于通過電感的儲能和續(xù)流,通過LC網(wǎng)絡(luò),將輸入端的正弦波脈寬調(diào)制方波進(jìn)行平滑,使電路的輸出端濾波電容器兩側(cè)得到標(biāo)準(zhǔn)平滑的正弦電壓波形。由于逆變器并網(wǎng)采用電流型控制模式,客觀上逆變器必須向電網(wǎng)輸出符合高次諧波法規(guī)的電流波形。逆變器的載波頻率為20 kHz左右,即便是大型發(fā)電站式光伏逆變器的載波頻率,也遠(yuǎn)遠(yuǎn)高于50 Hz的39次諧波(1950 Hz),因此,實質(zhì)上載波頻率的紋波并不會明顯影響高次諧波分量。也就是說,即便輸出濾波器中的濾波電感量很小,只要控制得當(dāng),調(diào)節(jié)好閉環(huán)電流控制參數(shù),并網(wǎng)時電流的高次諧波分量是不會太差的。然而實際情況似乎并不是如此,大多數(shù)情況下,在濾波電感量比較小時,往往會發(fā)現(xiàn)高次諧波分量也比較高。其主要原因是,當(dāng)輸出濾波器的感量偏低時,特別是當(dāng)電感量隨著電流的增長,出現(xiàn)感量大幅下降時,由于感量不是固定的常數(shù),閉環(huán)傳遞函數(shù)也不同;不注意的話小電感值有時還會導(dǎo)致系統(tǒng)采樣誤差、交流過零判別的不準(zhǔn)確??刂葡到y(tǒng)的閉環(huán)參數(shù)不匹配時,容易發(fā)生系統(tǒng)的振蕩,從而出現(xiàn)了較差的高次諧波。此時,電流波形的失真,常常還會伴隨出現(xiàn)比較大的音頻噪音。
解決這一問題有兩個截然不同的方法:
方法1:盡量提高濾波電感量,并盡量使電感保持一個固定值,使之不隨電流大小改變而改變。這種辦法的缺點(diǎn)是大幅增大了電感成本。目前中小功率光伏逆變器中廣泛采用的大容量非晶電感和大型發(fā)電站式逆變器中的硅鋼片類的電感均為這樣的考慮;
方法2:采用高性能低損耗、具有較大斜降特性的新型電感,通過調(diào)整閉環(huán)控制模型,優(yōu)化控制參量,使系統(tǒng)適應(yīng)高頻化、小感量的設(shè)計。通過提高系統(tǒng)的軟件控制水平,來取得更好的產(chǎn)品性價比,以提高產(chǎn)品技術(shù)核心競爭力。這一方法雖然難度較高,但符合電源技術(shù)的發(fā)展方向。
對于這種新型高效電感的設(shè)計,和Boost電感設(shè)計要求一樣,要求該電感在大紋波電流工作時,保持極佳的效率。由于其電感量可以設(shè)計成比較小的感值,即使要求直流內(nèi)阻較低,用銅量也能得到大幅的控制。對于磁性材料中的ΔB磁場變化率大的問題,同樣地采用Hybrid Magnetics技術(shù),可以控制磁性的損耗、減少漏磁的存在,達(dá)到很少的用銅量也能保持很低的內(nèi)阻的目的。
鑒于單相、3相交流線路上分別需要2個和3個相同感量的濾波電感,為了進(jìn)一步減小體積,提高磁性材料的利用率,還可以采用單相耦合式和3相耦合式電感設(shè)計的方案。
此外,對于大功率應(yīng)用,無論是Boost電感還是濾波電感,因其電感量偏小,電流紋波大的特點(diǎn),繞線的高頻集膚效應(yīng)和層間的接近效應(yīng)也會比較明顯,為此可采用長寬比大的方形扁銅線進(jìn)行立式繞制,最大限度改善其高頻損耗。
隔離型PV逆變器中的重要磁元件
隔離型光伏逆變器,由于增加了電氣隔離電路和元件,整機(jī)效率會有所下降,因此除了采用高效率的電路拓?fù)洌ㄈ鏛LC諧振、FB-ZVS移相全橋、有源鉗位反激電路等)外,其中高頻隔離變壓器、高效諧振電感的設(shè)計,也起著關(guān)鍵的作用。
對于采用有源鉗位反激拓?fù)涞母綦x大功率變壓器的設(shè)計,變壓器的低損耗設(shè)計極為關(guān)鍵。對于接近20 kHz或更高的工作頻率,磁芯元件必須是高頻損耗極好的高性能鐵氧體磁芯。而反激變壓器實質(zhì)上是一個儲能電感,需要很大的氣隙進(jìn)行能量的存儲,為此設(shè)計這類的變壓器時必須要遵循下列原則:
1)采取類似圖10所示的多段均勻氣隙以減小磁芯的漏磁;
2)采用合適線徑的多股漆包線繞制以盡可能減小銅線的渦流損耗和集膚效應(yīng);
3)采用有利于減輕漏感和繞組接近效應(yīng)的繞線結(jié)構(gòu)
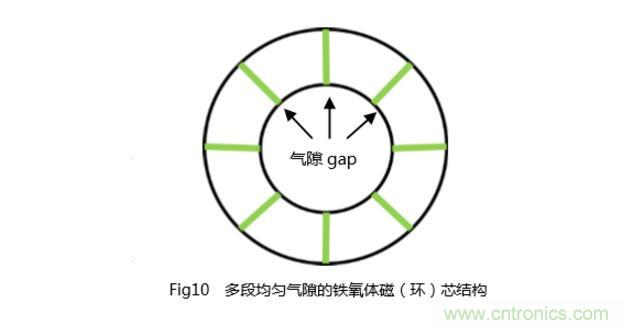
對于LCC諧振和FB-ZVS移相全橋的電路拓?fù)?,較好的設(shè)計手法是在隔離型功率變壓器設(shè)計時,盡可能地較少漏感的存在,以提高變壓器的效率,改善其生產(chǎn)工藝性;而把需要的諧振電感量外置,使用高效獨(dú)立的專用諧振電感來達(dá)到控制成本提高整機(jī)效率的目的。此外,由于LLC電路和FB-ZVS電路的工作模式大不相同,因此在設(shè)計LLC諧振電感和FB-ZVS諧振電感式時,應(yīng)考慮到其不同的損耗模型而進(jìn)行不同的設(shè)計側(cè)重,一般即便是同樣功率同樣電感量的產(chǎn)品,因其損耗模型不同,也不好互換使用。
光伏電感的電磁兼容性問題
在光伏逆變器中作為儲能元件的Boost電感以及作為濾波用的AC電感,一個共同的特點(diǎn)就是其電感的一端必然和功率半導(dǎo)體的高壓開關(guān)相連接。為了降低逆變器的開關(guān)損耗,除了采用過零軟開關(guān)技術(shù)以外,普遍的辦法就是盡量提高功率器件的驅(qū)動開通和驅(qū)動關(guān)閉的速度。這樣,電感的這一端不可避免地出現(xiàn)了極高的dV/dt的電壓變化。由于結(jié)構(gòu)上的原因,電感繞線的每相鄰匝間、層間等各個部位實際上分布了復(fù)雜的寄生電容和匝間結(jié)合漏磁造成的漏感,這些微小的電容和電感一起形成了一個非常復(fù)雜的LCR網(wǎng)絡(luò),當(dāng)電感的一端受到強(qiáng)烈的階躍電壓激勵時,電感內(nèi)部形成了復(fù)雜的高頻衰減諧振,其頻率一般會分布在十幾MHz~數(shù)百M(fèi)Hz的頻帶范圍,并具有一定的振蕩能量,這是光伏逆變器EMI的另一個重要干擾源。
為了消除其影響,被動的方法是,不得不在輸入輸出濾波回路中采用非常昂貴的共模濾波器,并由于共模濾波器要達(dá)到足夠的感量,從而使用了大量的銅繞線,進(jìn)一步增加了成本,降低了效率。
鑒于上述原因,在設(shè)計光伏Boost電感、AC濾波電感、隔離型高頻功率反激變壓器時,優(yōu)化電感的結(jié)構(gòu)、減輕其高頻振蕩源,將是高性能光伏電感必不可缺的要求。
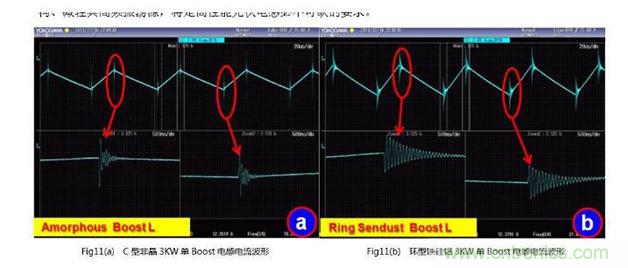
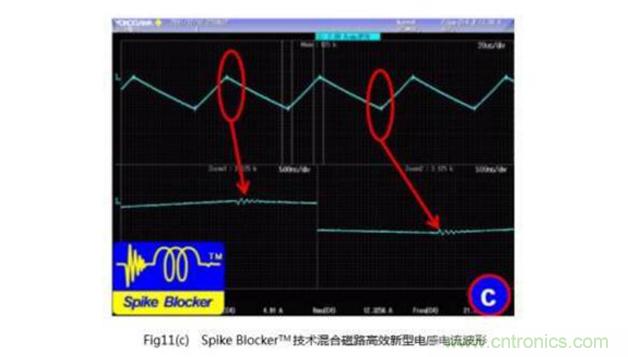
圖11(a)為目前廣為采用的C型非晶材料繞制的3 kW單Boost電感的額定功率時的典型工作電流波形。在Boost開通和關(guān)斷時,電感電流出現(xiàn)了比較嚴(yán)重的高頻振蕩,其振蕩頻率成分也比較豐富,約在20~30 MHz寬帶上;Fig11(b)為采用數(shù)只φ47的鐵硅鋁磁環(huán)繞制的3 kW單Boost電感的波形,同樣圖中顯示出10 MHz左右的高頻衰減振蕩;Fig11(C)則為采用了優(yōu)化結(jié)構(gòu)和相關(guān)設(shè)計工藝規(guī)范的Spike Blocker TM技術(shù)后,使用Hybrid Magnetics混合磁路設(shè)計的新型高效能電感的實測波形(這些測試均基于相同設(shè)備、相同輸入輸出電壓、功率、工作頻率條件),由此可見,關(guān)注電感的EMC設(shè)計工藝規(guī)范具有十分重要的意義。
光伏逆變器電感的技術(shù)發(fā)展趨勢
光伏逆變器中的電感,無論就其成本和效率影響來看,均在逆變器元件中占據(jù)著舉足輕重的地位,電感技術(shù)的進(jìn)步將極大地推動光伏技術(shù)的發(fā)展。
從微逆變器到發(fā)電站光伏逆變器,一個先進(jìn)的光伏電感設(shè)計,應(yīng)當(dāng)是在充分理解和結(jié)合光伏逆變器電路工作原理及特點(diǎn)的基礎(chǔ)上,充分發(fā)揮材料界可量產(chǎn)化的各種磁材料的優(yōu)點(diǎn),融合當(dāng)今電力電子領(lǐng)域有關(guān)磁集成及混合磁路等技術(shù),同時還須關(guān)注電磁兼容相兼顧的先進(jìn)工藝和產(chǎn)品設(shè)計理念。
電力電子技術(shù)發(fā)展的一個重要方向是通過新材料、新元器件、電路拓?fù)浼夹g(shù)、數(shù)字化技術(shù)、仿真控制技術(shù)等的不斷發(fā)展,實現(xiàn)電力變換的高性能、低成本化。而表征這一進(jìn)程的就是電源開關(guān)頻率的高頻化。因此,電感元件的小電感量化應(yīng)用趨向、高頻化、大紋波時也能保持低損耗的技術(shù),將成為推動這一進(jìn)程的重要力量。
可以預(yù)見,隨著這些電感技術(shù)的發(fā)展,1.5~50 kW中小功率光伏逆變器、250~500 kW的大型發(fā)電站集中式單機(jī)光伏系統(tǒng),將以更高的性能、更低的成本,分別從20 kHz向50 kHz、從3~4 kHz向10 kHz以上頻率的切換的步伐會越來越快。